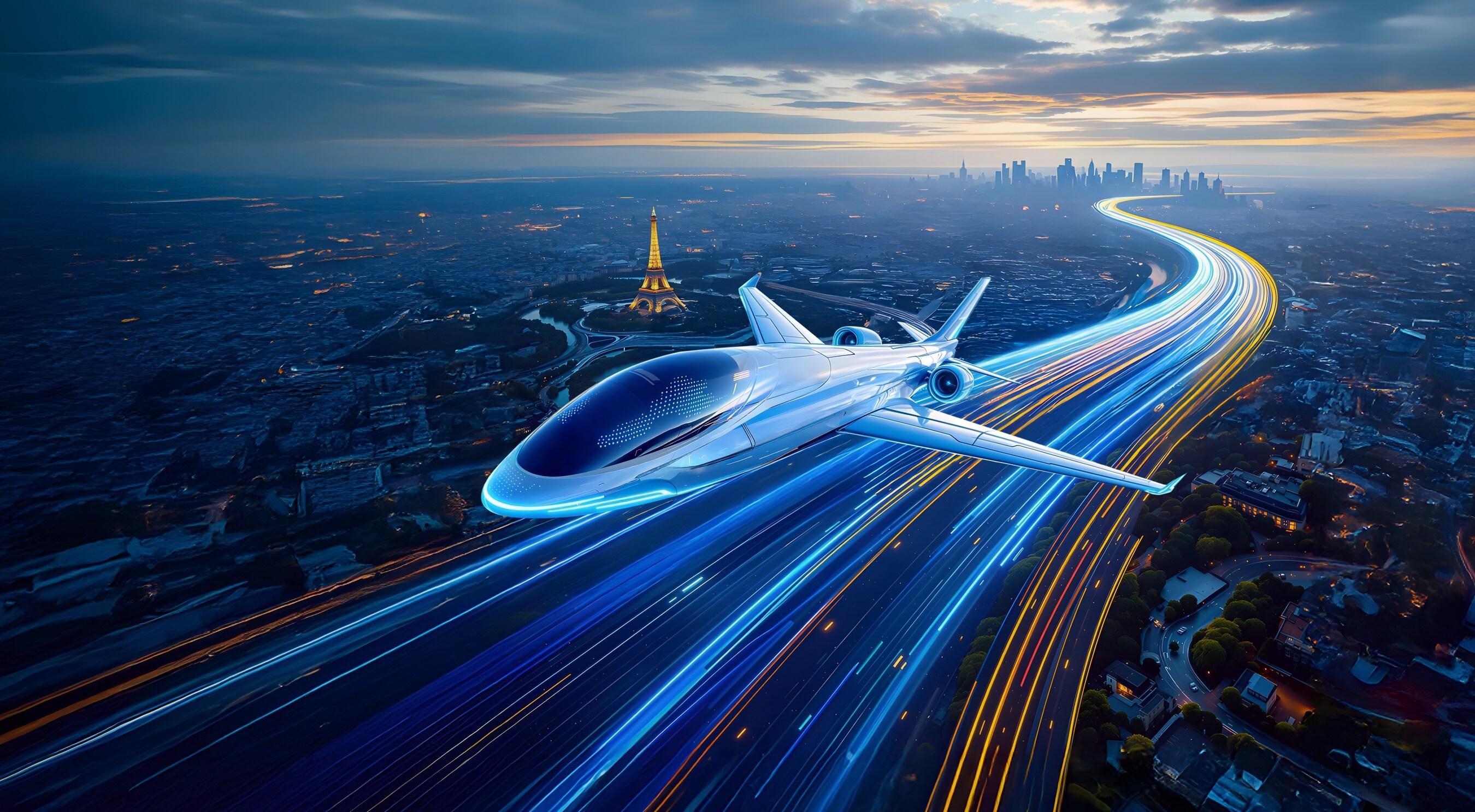
Source: businesswire | Published on: Friday, 15 November 2024
STERLING, Va.--(BUSINESS WIRE)--The U.S. Department of Energy (DOE)’s Office of Energy Efficiency and Renewable Energy has awarded circular manufacturing & robotics company Molg a $5 million grant for the Bipartisan Infrastructure Legislation (BIL) Novel Design for Disassembly Toolchains and Deployable Robotic Cells Project. This initiative focuses on developing an AI-enabled circular demanufacturing platform for consumer laptops, designed to harvest batteries 50 percent faster and at half of the cost of current state-of-the-art processes. The project was selected as part of the DOE’s Battery Recycling, Processing, and Collection Funding Opportunity, a $125 million funding initiative under the Bipartisan Infrastructure Law to improve consumer battery recycling programs.
Beyond enhancing the circularity of laptop batteries, Molg aims to set a new sustainability standard for all consumer electronics products. Molg’s approach starts with circular product design. The project will fund the development of a Design for Disassembly (DfD) Toolchain software to streamline the design process. The toolchain's parametric design module will enable predictable, repeatable disassembly sequences that can be performed autonomously, reducing complexity and cost. This lifecycle approach supports the transition to a domestic supply chain for critical materials, significantly improving the efficiency of battery reclamation.
“The U.S. needs to improve the cost and efficiency of battery recycling to secure its supply chain for sustainable electronics products,” said Molg CEO & Co-founder Rob Lawson-Shanks. “Robotics in circularity will significantly reduce operational costs while improving workforce safety and supporting green job growth. This project aims to show how to use cutting edge automation with Molg Microfactories to create scalable recovery of critical minerals, as well as going further and making it easier to design devices for circularity and automation from the beginning.”
With DOE funding, Molg will deploy five robotic “Microfactories” to dismantle commonly used laptops onsite with leading electronics disposition partners. Building on its existing collaboration to dismantle servers, Molg will launch its first microfactory under this program to a facility operated by Sims Lifecycle Services.
“The market is demanding flexible capacity to decommission IT assets to extend the life of devices and components,” said Sean Magann, chief commercial officer at Sims Lifecycle Services. “We are excited to participate with Molg to identify opportunities to recover more value on behalf of our clients and create sustainable models to reduce the need for virgin materials.”
Molg will also collaborate with leading consumer electronics OEMs, including HP, to leverage its DfD Toolchain to develop new laptop designs for enhanced circularity. The Toolchain, integrated into computer-aided design software, will enable data-driven insights and structures to guide the creation of sustainable product designs. Paired with the Microfactories, the DfD toolchains will be critical to achieving product circularity and helping advance partners’ sustainability goals, like HP’s goal of reaching 75% circularity for products and packaging by 2030.
"HP is excited to join forces with Molg to accelerate a future where electronic products are born with circularity in mind," said Loretta Li-Sevilla, Global Head of Future of Work and Service Enablement, HP Inc. "Integrating the DfD Toolchain into our processes brings us closer to designing laptops that can be easily disassembled and recycled, advancing our commitment to reduce e-waste and build a more sustainable world."
Finally, Molg is partnering with Virginia Commonwealth University (VCU) and Rewriting the Code to support workforce development, especially among underrepresented populations. Together, these groups will develop curriculum and training materials to prepare 10 robot technicians and 5 sustainable product designers for careers in the circular economy. Over time, robotics will accelerate green job growth in the recycling, manufacturing, and product design, making jobs more efficient and lucrative for workers.
Manually dismantling electronics can be hazardous to workers and costly, and global e-waste recycling rates remain low. Only 22.3% of e-waste was recycled in 2022, according to data from the UN Global E-waste Monitor, while consumer demand for electronics continues to surge, with 241.8 million PCs shipped worldwide in 2023 according to Gartner.
By investing in a skilled workforce for advanced demanufacturing, Molg aims to create safer, higher-paying jobs while lowering recycling costs. As demand grows for reclaimed materials and a resilient domestic battery supply chain, a trained workforce in sustainable design and advanced technologies will be essential to scale these sustainable solutions.
"VCU's Supply Chain Management and Analytics Department is proud to partner with Molg on this grant," said David Berdish, Director of the Circular Minerals Resilience project. "Our team is eager to develop supply chain methods and train the workforce needed to ensure critical minerals in electronics and batteries are recycled for a more affordable, equitable, and sustainable future."
The project is one of seven projects selected under “Topic 2” of the grant program, which aims to improve the economics of recycling consumer electronics batteries in order to spur the market for battery recycling. Other topic areas focused on expanding consumer participation in recycling programs, establishing retailer programs for battery collection and transport, and developing state & local programs for enhanced collection, recycling, and reprocessing. Across all topic areas, a total of 19 projects were selected to participate in the program.
The DOE grant funding coincides with the announcement of Molg closing its $5.5m seed funding round with Closed Loop Partners, Amazon Climate Pledge Fund, ABB Robotics and Automation Ventures, Overture, Elemental Impact, and Techstars.
About Molg
Molg tackles the growing e-waste problem by making manufacturing circular. The company’s robotic microfactory can autonomously disassemble complex electronic products like laptops and servers, helping keep valuable components and materials within supply chains and out of landfills. Molg partners with leading electronics manufacturers to design the next generation of products with reuse in mind, ensuring that one product’s end is another’s beginning. To learn more, visit molg.ai.